Crucial Factors To Consider for Repairing and Repairing Your Packaging Device
When addressing the complexities of troubleshooting and repairing your packaging maker, numerous essential elements need to be considered to make sure both performance and safety and security. From understanding common mechanical and electrical problems to utilizing ideal analysis devices, each action plays an essential role in preserving operational stability. In addition, adherence to safety and security methods and making use of OEM parts can substantially influence efficiency. Yet, many neglect the complexities of routine maintenance and paperwork, which are necessary in protecting against future difficulties. What other crucial elements could be the trick to boosting your maker's dependability?
Understanding Usual Problems
Identifying usual problems in product packaging makers is vital for keeping functional efficiency and decreasing downtime. Packaging equipments, important to assembly line, can encounter a variety of troubles that impede their efficiency. One prevalent concern is mechanical malfunction, commonly resulting from deterioration on components such as gears and belts, which can cause inconsistent packaging quality.
One more usual issue is imbalance, where the packaging products might not align correctly, creating jams or incorrect sealing. This misalignment can originate from incorrect configuration or changes in product specifications. In addition, electric failures, such as defective sensors or control systems, can interfere with the device's automated processes, resulting in production hold-ups.
Operators may also experience difficulties with software problems, which can impact machine programming and performance. Furthermore, inadequate maintenance methods commonly add to these issues, emphasizing the need for regular evaluations and timely service treatments. By recognizing these usual issues, drivers can apply aggressive measures to ensure peak efficiency, therefore lowering pricey downtimes and boosting general efficiency in packaging operations.

Diagnostic Devices and Techniques
Efficient troubleshooting of packaging makers relies greatly on a variety of analysis devices and methods that promote the identification of underlying concerns - packaging machine repair service. One of the main devices is making use of software program diagnostic programs, which can keep an eye on machine efficiency, analyze error codes, and give real-time data analytics. These programs make it possible for service technicians to determine particular breakdowns promptly, substantially decreasing downtime
Along with software remedies, oscilloscopes and multimeters are necessary for electric diagnostics. Multimeters can determine voltage, existing, and resistance, aiding to identify electrical faults in circuits. Oscilloscopes, on the other hand, supply visualization of electric signals, making it less complicated to spot irregularities in waveforms.
Mechanical problems can be identified making use of resonance evaluation devices and thermal imaging electronic cameras. Vibration analysis permits the discovery of inequalities or imbalances in equipment, while thermal imaging aids identify overheating components that may lead to mechanical failure.
Lastly, visual assessments, incorporated with basic checklists, stay very useful for standard troubleshooting. This thorough approach to diagnostics ensures that specialists can successfully attend to a vast array of concerns, thereby enhancing the reliability and performance of packaging machines.
Security Protocols to Comply With
Exactly how can product packaging equipment drivers make certain a risk-free functioning atmosphere while fixing? The implementation of strict safety and security methods is necessary. Operators must begin by separating the maker from its power source before initiating any type of troubleshooting procedures. Lockout/tagout (LOTO) methods have to be imposed to prevent unintended re-energization during upkeep.
Operators should likewise familiarize themselves with the device's security functions, such as emergency stop buttons and safety guards, verifying that they are functional before starting any diagnostic work. packaging machine repair service. It is important to interact with employee, ensuring all personnel are conscious of the ongoing troubleshooting activities
Finally, drivers must record all treatments and searchings for, offering a clear record in situation of future concerns. By sticking to these security protocols, product packaging equipment drivers can create a safer setting, lessening dangers while successfully fixing and repairing machinery.
Components Substitute Guidelines
When it comes to keeping packaging machines, recognizing components replacement standards is necessary for guaranteeing optimal efficiency and durability. Frequently assessing damage on device components is critical, as timely replacements can protect against extra considerable damages and pricey downtime.
First of all, always describe the maker's requirements for suggested substitute intervals and component compatibility. It is essential to make use of OEM (Original Devices Manufacturer) parts to assure that replacements fulfill the required top quality and performance criteria.
Before starting any kind of replacement, make sure the equipment is powered down and effectively locked out to avoid unintentional activation. Record the condition of the replaced parts and the date of substitute, as this will help in monitoring maintenance patterns with time.
Additionally, examine the surrounding components for indications of wear or possible issues that may emerge from the substitute. This holistic approach can alleviate future troubles and improve functional performance.
Last but not least, after replacing any parts, conduct detailed testing to ensure that the device is working properly which the brand-new elements are incorporated flawlessly. Following these standards will i was reading this certainly not just expand the life of your product packaging machine yet also improve overall productivity.
Upkeep Best Practices
Constant maintenance practices are important for maximizing the efficiency and life-span of product packaging equipments. Developing a detailed upkeep routine is the very first step toward ensuring optimum efficiency. This routine ought to include daily, weekly, and month-to-month jobs customized to the certain maker and its operational demands.
Daily checks ought to concentrate on vital elements such as sensing units, belts, and seals, guaranteeing they are clean and functioning correctly. Weekly upkeep may include examining lubrication levels and tightening up loosened fittings, while monthly jobs need to consist of extra thorough examinations, such as placement checks and software updates.
Utilizing a checklist can simplify these procedures, making certain no important tasks are ignored. Furthermore, keeping accurate records of upkeep activities assists recognize repeating problems and educates future methods.
Training personnel on correct usage and handling can substantially reduce deterioration, protecting against unnecessary failures. Additionally, spending in high-quality parts and lubricating substances can boost machine performance and dependability.
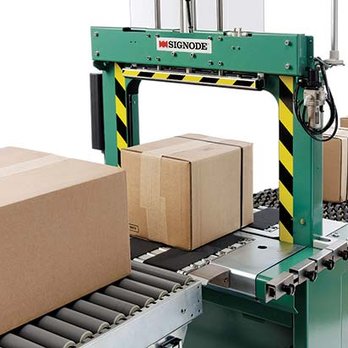
Final Thought
To conclude, reliable fixing and repair work of product packaging equipments require an organized technique encompassing safety and security procedures, the use of appropriate analysis tools, and adherence to upkeep finest methods. Timely components and normal examinations replacement with OEM components play an essential role in maintaining maker performance and integrity. Furthermore, meticulous paperwork of treatments and findings adds to a much deeper understanding of repeating concerns, ultimately improving functional efficiency and minimizing the chance of future malfunctions.
When dealing with the intricacies of troubleshooting and fixing your product packaging machine, several essential factors should be thought about to make certain both performance and safety.Identifying common problems in packaging makers is necessary for keeping functional performance and minimizing downtime.Effective troubleshooting of packaging machines relies heavily on a variety of diagnostic devices and techniques that facilitate the recognition of description underlying concerns.Just how can product packaging equipment drivers ensure a secure functioning setting while repairing?In verdict, efficient read the full info here fixing and repair service of product packaging makers require a structured approach encompassing safety protocols, the usage of appropriate analysis devices, and adherence to upkeep ideal methods.